電動(dòng)汽車電池管理系統(tǒng)使用柔性 PCB 時(shí),激光焊接產(chǎn)生的機(jī)械應(yīng)力和溫度變化會(huì)導(dǎo)致表面貼裝 NTC 熱敏電阻熱開裂,這是一種難以預(yù)測(cè)的潛在嚴(yán)重故障。采用軟端子和塊狀金屬氧化物工藝的貼片熱敏電阻可最大限度減小元件開裂的風(fēng)險(xiǎn)。
隨著電動(dòng)汽車 (EV) 市場(chǎng)的持續(xù)快速增長,技術(shù)挑戰(zhàn)和為應(yīng)對(duì)這些挑戰(zhàn)而開發(fā)的創(chuàng)新也在不斷發(fā)展。在這些挑戰(zhàn)和創(chuàng)新當(dāng)中,改進(jìn)電池技術(shù)、提高電源電路效率和快速充電解決方案是設(shè)計(jì)工程師最為關(guān)注的領(lǐng)域。
目前,電動(dòng)汽車主要使用鋰離子電池,單體電池電壓為 3.6 V 至 3.7 V。因此,建立一個(gè)總電壓為 500 V 至 900 V 的動(dòng)力系統(tǒng)需要串并聯(lián)數(shù)百個(gè)這樣的電池。此外,優(yōu)化如此多電池單元構(gòu)成的系統(tǒng)的性能需要高效電池管理系統(tǒng) (BMS),這種系統(tǒng)必須能夠監(jiān)測(cè)電池的溫度、阻抗 (電池內(nèi)阻)、電壓以及充放電電流。其中每項(xiàng)指標(biāo)都會(huì)影響電池的性能。
BMS 一般包括電池單元管理控制器 (CMC),主控中央單元或電池管理控制器 (BMC)。 CMC 采用多通道 IC (目前最多配備 16 通道) 執(zhí)行監(jiān)控功能,BMC 負(fù)責(zé)控制每個(gè) CMC。這類系統(tǒng)測(cè)量的主要參數(shù)包括溫度、阻抗、電壓和電流。在考慮溫度測(cè)量的情況下,負(fù)溫度系數(shù) (NTC) 熱敏電阻是最常用的元件解決方案。通常,NTC 熱敏電阻緊貼電池或模塊壁,或電氣接點(diǎn)連接以確定“熱點(diǎn)”溫度。隨著熱敏電阻溫度上升,具有高靈敏度的 NTC 的阻值會(huì)下降,因?yàn)?NTC 電阻具備較大的負(fù)溫度系數(shù)。溫度的測(cè)量是通過采集普通電阻+熱敏電阻的電阻網(wǎng)絡(luò)上的電壓,并將該模擬電壓信號(hào)輸送到集成在 IC 里面的 ADC 轉(zhuǎn)換器進(jìn)行后續(xù)處理完成的。精確的溫度采集對(duì)電池的正常運(yùn)行和整個(gè) BMS 系統(tǒng)的安全來說必不可少。為了能精準(zhǔn)地測(cè)量到溫度,NTC 和測(cè)量電路又顯得尤為重要。
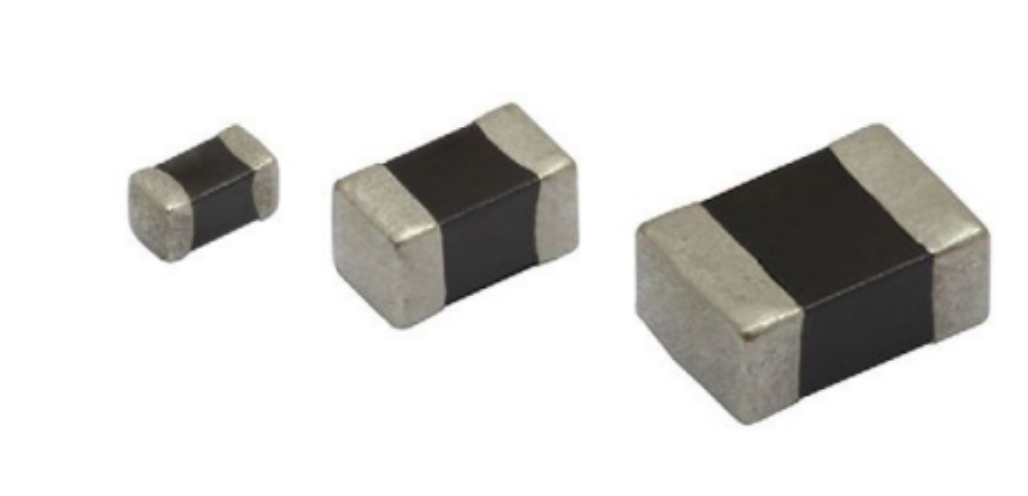
高壓電池系統(tǒng)可以包括二十個(gè)或更多表面貼裝 NTC 熱敏電阻,這些熱敏電阻位于包裹在組裝的電池結(jié)構(gòu)的柔性電路上。如果安裝基板是 FR4 PCB,這些元件可以進(jìn)行回流焊或波峰焊。

然而,一些柔性電路不能使用這些焊接技術(shù),而是依靠局部加熱的激光焊接,以避免損壞其他敏感部件。如果不能嚴(yán)格控制這種激光焊接工藝,就會(huì)導(dǎo)致陶瓷元件受到過量的熱應(yīng)力而開裂。同樣,整個(gè)電池系統(tǒng)在組裝和工作中也會(huì)受到很大的機(jī)械應(yīng)力。而且柔性電路板上的組件也會(huì)受到通過器件端子傳導(dǎo)的扭力的影響,有些情況下甚至器件本身會(huì)直接承受壓力,這些情況都會(huì)導(dǎo)致器件結(jié)構(gòu)開裂。
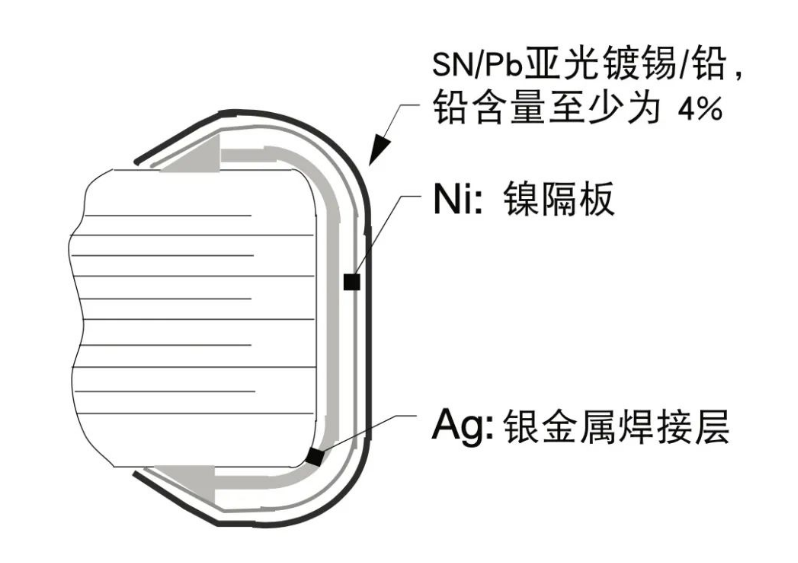
這種故障取決于多種因素,使其難以檢測(cè),并且不太可能提前預(yù)測(cè)故障的出現(xiàn)。此外,多層陶瓷電容已經(jīng)充分證明,實(shí)際元件故障 (元件開裂) 可能在系統(tǒng)完成安裝部署之后的很長一段時(shí)間才出現(xiàn)。這種故障也可能是災(zāi)難性的,使得更換/維修的代價(jià)非常高。為降低溫度變化或使用柔性 PCB 可能產(chǎn)生的機(jī)械應(yīng)力導(dǎo)致元件開裂的風(fēng)險(xiǎn),Vishay NTCS 系列熱敏電阻采用塊狀金屬氧化物材料,配有固化環(huán)氧樹脂封裝的鎳-錫鍍層聚合物端子,而不是采用燒結(jié)的厚膜材料。這種解決方案提供柔性端子結(jié)構(gòu),其應(yīng)力測(cè)試期間的表現(xiàn)顯著優(yōu)于其他端子材料,同時(shí)也顯著優(yōu)于來自于其它制造商的多層陶瓷結(jié)構(gòu)器件的柔性端子方案。由于使用柔性 PCB 電路板的電池管理系統(tǒng)的各個(gè)組件承受的應(yīng)力不盡相同,因此采用能夠吸收扭力和熱應(yīng)力的柔性端子解決方案可以顯著減少潛在的現(xiàn)場(chǎng)實(shí)地故障,從而提高可靠性和使用壽命。
BMS核心芯片封裝清洗:
合明科技研發(fā)的水基清洗劑配合合適的清洗工藝能為芯片封裝前提供潔凈的界面條件。
水基清洗的工藝和設(shè)備配置選擇對(duì)清洗精密器件尤其重要,一旦選定,就會(huì)作為一個(gè)長期的使用和運(yùn)行方式。水基清洗劑必須滿足清洗、漂洗、干燥的全工藝流程。
污染物有多種,可歸納為離子型和非離子型兩大類。離子型污染物接觸到環(huán)境中的濕氣,通電后發(fā)生電化學(xué)遷移,形成樹枝狀結(jié)構(gòu)體,造成低電阻通路,破壞了電路板功能。非離子型污染物可穿透PC B 的絕緣層,在PCB板表層下生長枝晶。除了離子型和非離子型污染物,還有粒狀污染物,例如焊料球、焊料槽內(nèi)的浮點(diǎn)、灰塵、塵埃等,這些污染物會(huì)導(dǎo)致焊點(diǎn)質(zhì)量降低、焊接時(shí)焊點(diǎn)拉尖、產(chǎn)生氣孔、短路等等多種不良現(xiàn)象。
這么多污染物,到底哪些才是最備受關(guān)注的呢?助焊劑或錫膏普遍應(yīng)用于回流焊和波峰焊工藝中,它們主要由溶劑、潤濕劑、樹脂、緩蝕劑和活化劑等多種成分,焊后必然存在熱改性生成物,這些物質(zhì)在所有污染物中的占據(jù)主導(dǎo),從產(chǎn)品失效情況來而言,焊后殘余物是影響產(chǎn)品質(zhì)量最主要的影響因素,離子型殘留物易引起電遷移使絕緣電阻下降,松香樹脂殘留物易吸附灰塵或雜質(zhì)引發(fā)接觸電阻增大,嚴(yán)重者導(dǎo)致開路失效,因此焊后必須進(jìn)行嚴(yán)格的清洗,才能保障電路板的質(zhì)量。
合明科技運(yùn)用自身原創(chuàng)的產(chǎn)品技術(shù),滿足芯片封裝工藝制程清洗的高難度技術(shù)要求,打破國外廠商在行業(yè)中的壟斷地位,為芯片封裝材料全面國產(chǎn)自主提供強(qiáng)有力的支持。
推薦使用合明科技水基清洗劑產(chǎn)品。